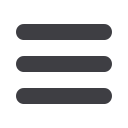
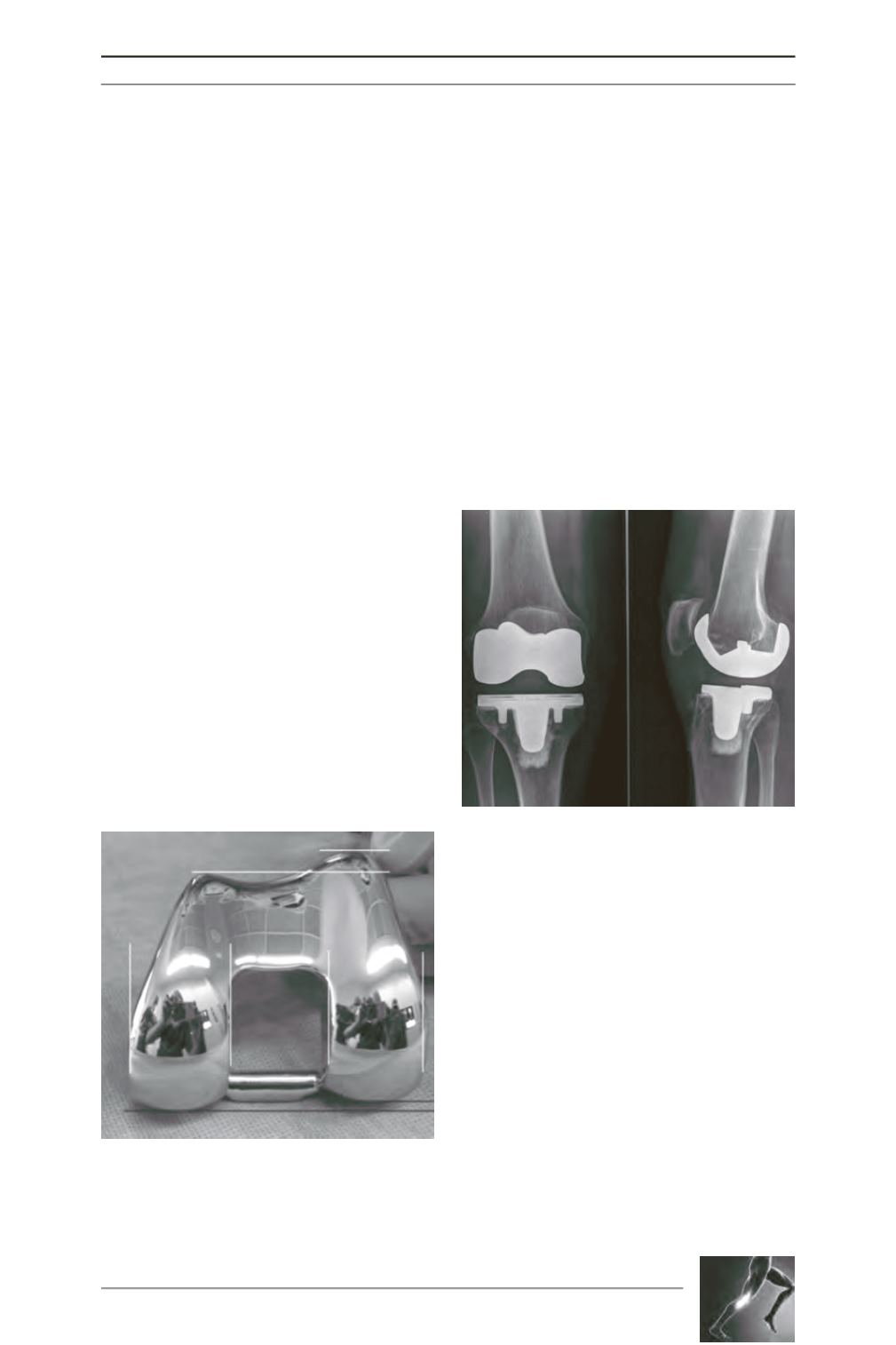
The reasons for a customized knee prosthesis Stepping outside the Square
87
Manufacturing process
In order to confirm the feasibility of such a
project, we performed a limited series of
12 customized patient specific postero-
stabilized total knees with a fixed bearing, after
appropriate patient consent. Out of this
preliminary experience we were able to
demonstrate that the cutting guides were
accurate and that the prostheses could
accurately match the native knee. We do believe
that building a customized implant is achievable
(fig. 7, 8).
The real challenge is then to demonstrate a
clinical relevance and durable advantage of
this option in every surgeon’s hands compared
to the modern range of implants. So far none of
the current attempts have yet produced
consistent published results.
Generalizing the process is another challenge.
The implant design process requires several
steps that cannot all be automated so far,
including; clearance of osteophytes, estimation
of cartilagewear, establishing suitedkinematics,
positioning of the posterior stabilization cam
and alignment of the segments, etc. An
individual surgeon cannot be asked to give his
contribution for every single case plan. As such
there is a need for detailed algorithm based
upon large patient anatomic bases crossed with
the design features.
Whether the image generation is CT based or
MRI based is still a subject of debate. Also,
collecting data with reliable imaging and
transferring them in a safe way is another vast
investment. Finally the manufacturing process
is an additional new challenge: one cast for one
patient is not currently a sustainable solution.
Selectingtheidealandaffordablemanufacturing
process along with subsequent specification
requirements and legal compliance issues is
not an insignificant hurdle.
Conclusion
Custom made implants offer a chance to
significantly improve both the life of the patient
and the job of the surgeon. This fascinating
adventure is a rather complex challenge.
Ultimately, mailed delivery of a personalized
implant, along with its specific disposable
instrumentation in a single box will be a major
improvement for the manufacturer, the surgical
institutions and the payers. The question
remains: is the initial investment worth the
potential benefit? It is likely that successful
surgical pioneers would agree!
Fig. 7: Customized femoral implant. The distal and
posterior contours are symmetrical and in line with
the tibial tray, but the condyles are not identical
and replicate the native sagittal condylar contours
and respective sizes.
Fig. 8: One year postoperative radiograph of a right
customized TKR in an young and active female
patient.