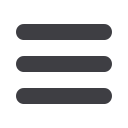
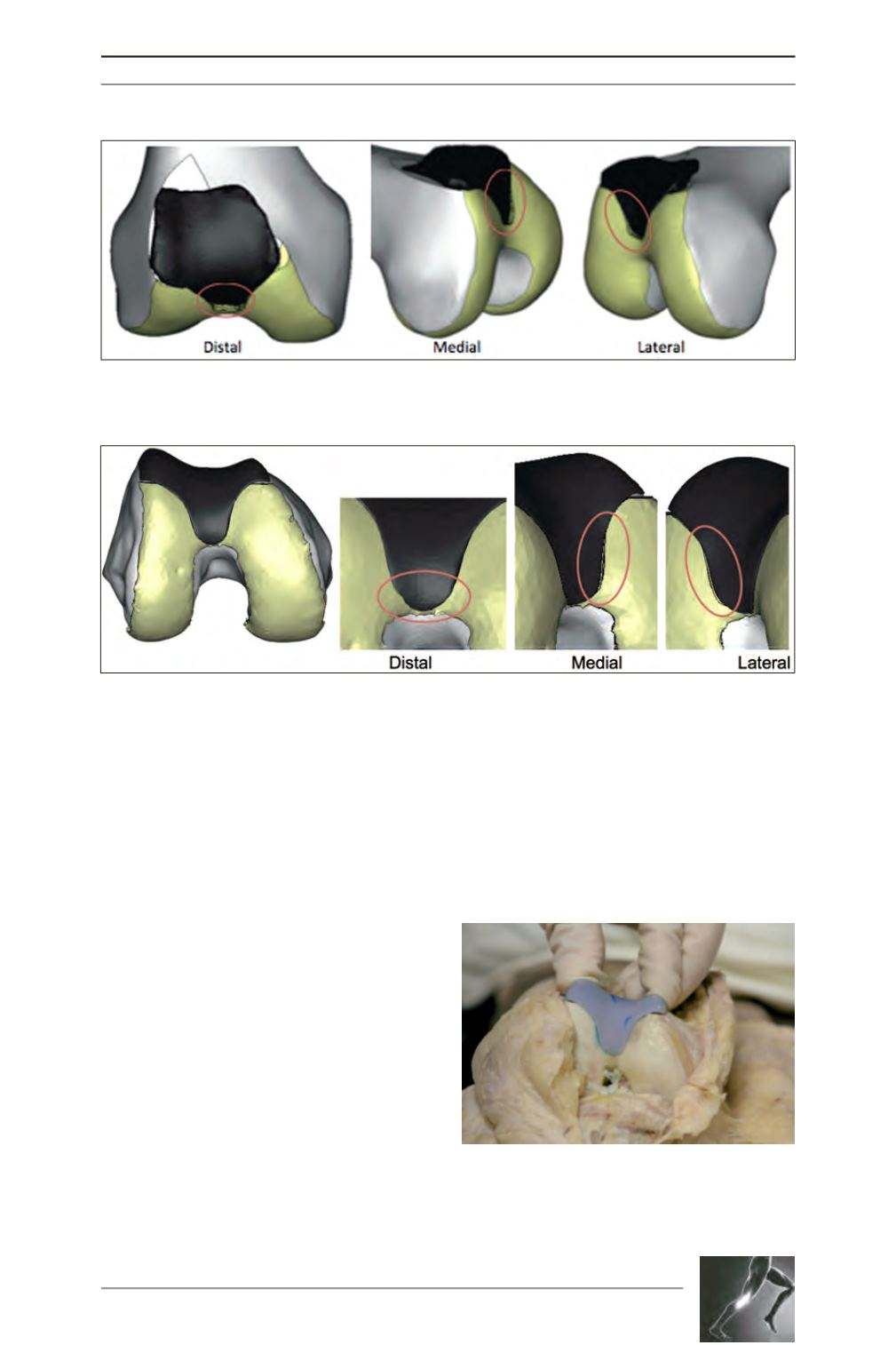
Robotic surgery and intelligent intruments - Patellofemoral Arthroplasties
53
When doing preoperative planning, it becomes
evident that in certain severe trochlea dysplasia
cases it is impossible to fit any of the off the
shelf commercially available prosthesis to the
trochlea (fig. 6). In these cases the option is to
consider a TKR rather than a PFR or to design
a patient-specific prosthesis. Patient-specific
prostheses need to be designed within
predetermined parameters concerning things
like; the trochlear angle; trochlear depth;
medial-lateral dimension; and medial and
lateral anterior-posterior dimensions (fig. 7).
At present the patient-specific prosthesis
manufactured by CNC (computer numerical
control) techniques are relatively slow and
expensive because, the machines have to be
specifically calibrated and set up tomanufacture
a single part. In future use it will be made of
rapid or additive manufacturing, which are
already in use in the aeronautical industry. As
the costs come down, it would become an
attractive option because these machines are
particularly suited for making once off products
(fig. 8).
Fig. 6: An example of the misfit between a commercially available off the shelf prosthesis on the femur. The
distal fit is compromised.
Fig. 7: Patient-specific prosthesis can ensure a smooth transition between the prosthesis and the patient’s
articular cartilage on distal, medial and lateral without compromising the trochlear groove alignment.
Fig. 8: Patient-specific PFR implantation was
performed using patient-specific instrumentation.
The prosthesis and the surgical instruments were
manufactured using rapid prototyping (additive
manufacturing).